棚番号・棚札を使った在庫管理(棚管理)の仕組みと始め方
棚管理とは、倉庫や店舗などにおける在庫の保管場所を明確に定めて、品目ごとに”どこにどれだけ存在しているのか”を把握するための管理手法です。「モノの置き場」をただ設けるだけでなく、棚ごとに保管された在庫を明確にして、在庫数の把握、入出庫やピッキングの効率性や正確性の向上を目的としています。
棚管理の基本
棚管理では「棚の位置情報」と「棚に置かれた在庫の情報」をあわせて管理することが大前提です。そのために不可欠な要素が棚番号と棚札(棚カード)です。
- 棚番号 = 場所を特定するための座標
- 棚札 = 棚の中身を示すカード
棚管理を始める際は、まずこの基本の組み合わせを整備することからスタートしましょう。
棚番号について

棚番号は、在庫の正確な位置を示すための識別コードです。作業者が迷わずピッキングや入庫処理を行えるように一目で分かる表記にしておくことが大切です。
一般的な棚番号の付け方
例:『A-03-2』 → Aエリア、3列目の2段目
倉庫内のエリア・列・段の順に表記するのが基本となります。英数字の組み合わせにすることで、一目で上下・左右・前後の方向が明確になります。このように体系的な棚番号を設定することで、それぞれの棚を管理・把握します。
棚札について
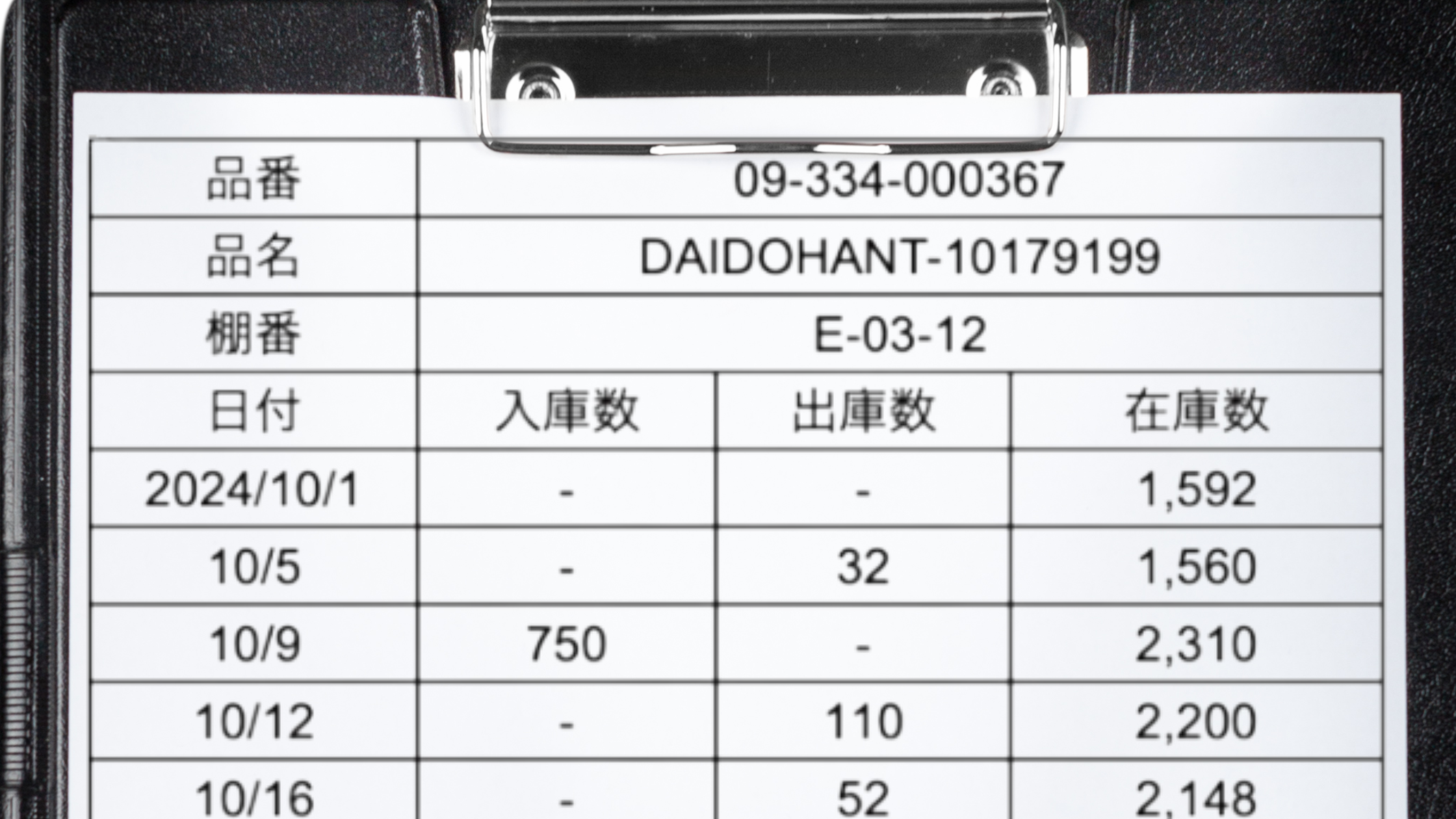
棚札は、棚に保管されている在庫の数量を品目ごとに分かりやすく明示するもので、手書きで書き加えられるように紙で管理している場合がほとんどです。システム化されていないアナログ管理の現場では、在庫情報の可視化において非常に有用です。
棚札に記載すべき情報
- 品番
- 品名(品目)
- 棚番(棚番号)
- 現在の在庫数
- 入出庫履歴(日付・数量)
棚札は誰が見ても在庫数がすぐに把握できるため、複数人でも管理・共有しやすいのが特徴です。また紙のためコストが安く、手軽に導入できます。
棚番号と棚札を用いた管理方法
棚管理を適切に行うためには棚番号と棚札を連動させることが基本です。棚番号で物理的な位置を明確にして、棚札で在庫情報や在庫数を記録します。
この組み合わせにより「どこに何があるのか」「どれだけあるのか」「最後にいつ入出庫したのか」といった情報を即座に確認できます。
棚管理における入出庫処理や在庫管理の仕方
・棚番号ごとに同一の在庫をまとめる
棚札は品目ごとに設置する
・入出庫時は棚札に記録する
作業者が在庫を動かした場合は棚札に入出庫数と日付を記載する
・総在庫数の把握
週次・月次で倉庫内の棚札を回収してExcelなどに転記する
・定期的に棚卸を行い実数と照合
把握している在庫数(理論在庫)と実在庫を比較して差異がないかを確認する
ただし品目が増えたり、保管場所が複雑化すると棚札だけでは管理が追いつかなくなるため、この仕組みをベースとしたシステム化が必要になります。
棚札の運用における課題
手書きによるミスの発生
手書きでの運用が中心となるため、書き間違いや読みづらさによるヒューマンエラーは避けられません。記入のタイミングや表記のばらつきも生じやすく、複数人で運用する現場では在庫情報の正確性が保ちにくくなります。
紛失や破損
棚札は紙で管理されることが多いため紛失や汚れ、破損によって判読不能になるリスクがあります。整理や在庫移動の際に外されたまま戻されないこともあり、湿気や埃の多い環境では劣化が早く長期間の使用には向きません。
保管場所が分かれていると把握しづらい
同じ在庫が複数の棚に分けて保管されている場合、個別で棚札を管理する必要があり、在庫数を把握するには手作業で計算しなければなりません。さらに、ピッキングの優先順が不明確でわかりづらいという課題があります。
棚管理に欠かせないロケーション管理の活用
棚管理を効率よく機能させるには「どこに、何を、どう置くか」というロケーション(保管場所)の設計と管理が不可欠です。
ロケーションを適切に設計することで、ピッキングミスの防止、在庫差異の削減、保管スペースの最適化など、在庫管理の精度とスピードが飛躍的に向上します。
以下では、代表的な3つの管理方式について解説します。
固定ロケーション管理
在庫ごとに決められた棚や保管場所を割り当てて管理する方式です。保管場所が変動しないため、作業者が一度覚えてしまえば迷うことなくピッキングや補充作業が行えます。定番商品や入出庫の頻度が高い品目を取り扱う場合に向いています。
向いているケース
- 定番商品、入出庫の頻度の高い品目を扱う場合
- SKU数(サイズ違い・色違い)が少なく、在庫の回転率が安定している場合
- 小規模倉庫や手作業での管理が中心である場合
メリット
- ピッキングのスピードが速い
- 誤出庫が起きにくい
デメリット
- 空きスペースが発生しやすく、保管効率が悪い
- 一時的に在庫量が増えても他の棚を使えず、柔軟性に欠ける
フリーロケーション管理
品目ごとの保管場所を固定せず、その都度空いている棚に在庫を配置する方式です。多品種少量で、なおかつ入出庫が頻繁な現場では限られたスペースを効率よく活用できます。季節によって在庫量が変動したり、突発的な大量入庫があるような業態でも、臨機応変に対応できる強みがあります。
ただし、フリーロケーション管理を行う際はアナログなやり方では限界があるためシステムを使った運用が推奨されています。
向いているケース
- SKUが多い / 入出庫が頻繁な場合
- EC物流やアパレル業界など、商品が常に入れ替わる場合
- 倉庫スペースを最大限活用したい場合
メリット
- デッドスペースが減る
- 在庫変動に強く、臨機応変な配置が可能
デメリット
- システムの導入が必須
- 棚番を常に記録・照会しないとピッキングできない
- ヒューマンエラーや誤配置リスクが高く、業務の標準化が困難
ダブルトランザクション方式
物流倉庫などで用いられるケースが多い方式で、ストックエリアとピッキングエリアを分けて在庫を管理します。ストックエリアにはケースやパレットなどの大きな荷姿の在庫を保管して、ピッキングエリアでは個装のものを中心に管理します。ピッキングエリアは固定ロケーションで行い、ストックエリアではフリーロケーションによる保管効率を重視した運用を行う企業が多いです。
向いているケース
- 大型倉庫を保有する場合
- 在庫量が多く、ピッキング効率とスペース効率の両立が求められる場合
- ロケーション管理やハンディターミナル対応のシステムが導入されている場合
メリット
- ピッキングは固定ロケーションで素早く行える
- 保管スペースはフリーロケーションで柔軟に運用可能
- 作業効率とスペース活用のバランスが取れる
デメリット
- 補充作業(ストック → ピッキング)の手間が発生
- 管理が煩雑になりやすく、管理システムとの連携が必須
- 品目の入れ替えや季節変動などに合わせたロケーションの設計が必要
棚管理もおまかせ!クラウドERP『キャムマックス』で実現する在庫管理
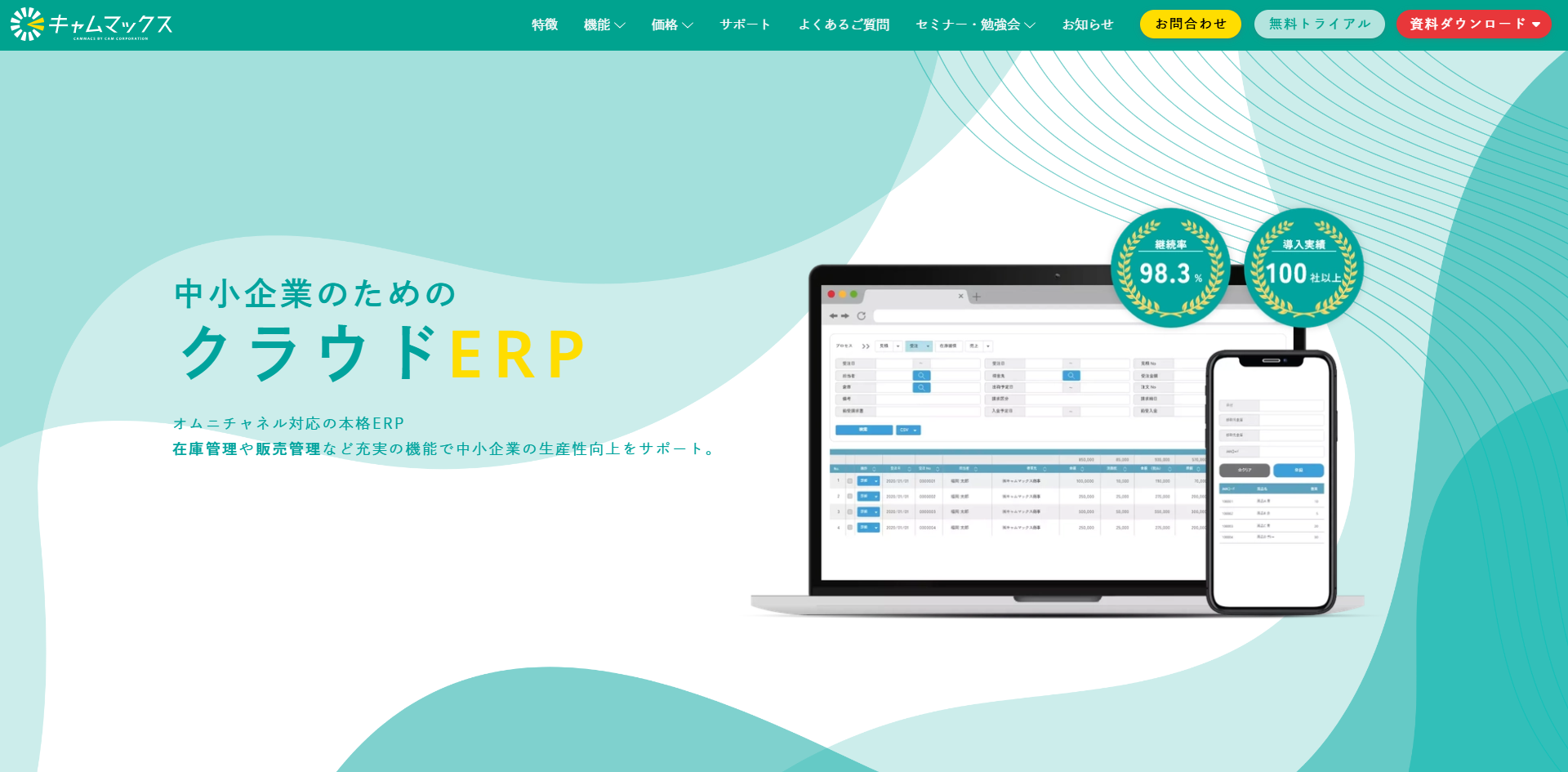
項目 | アナログ管理 | キャムマックス導入後 |
---|---|---|
棚番号管理 | 手書き・経験に頼った管理 | データベースで管理 |
在庫記録 | 手作業で記録・集計 | 入出庫時に自動反映 |
商品の場所確認 | 現場に行って確認 | システム上で一目瞭然 |
棚卸 | 目視・手集計 | スキャンで即照合が可能 |
作業の属人化 | 経験者に依存 | 誰でもできる仕組み化 |
従来のアナログな棚管理では、人による記録・確認・判断が前提でしたが「キャムマックス」の在庫管理機能を活用することで“誰でも正確にできる作業”へと変わります。
- 在庫の場所・数量・履歴を常に可視化
- ヒューマンエラーの削減・作業の標準化
- 複数拠点や外注倉庫の管理も一元化
- ピッキング指示・補充指示もシステム化できる
アナログな棚管理では、作業者が棚札に手書きで情報を記入して、棚に直接貼り付ける運用が基本でした。
これに対してキャムマックスでは、棚や品目ごとに付与されたバーコード(QRコード)を読み取ることで、情報の登録・更新を即座に行うことができます。
詳しくは、機能オプション『WMSモバイル』をご確認ください。
バーコードを使って在庫&ロケーション管理
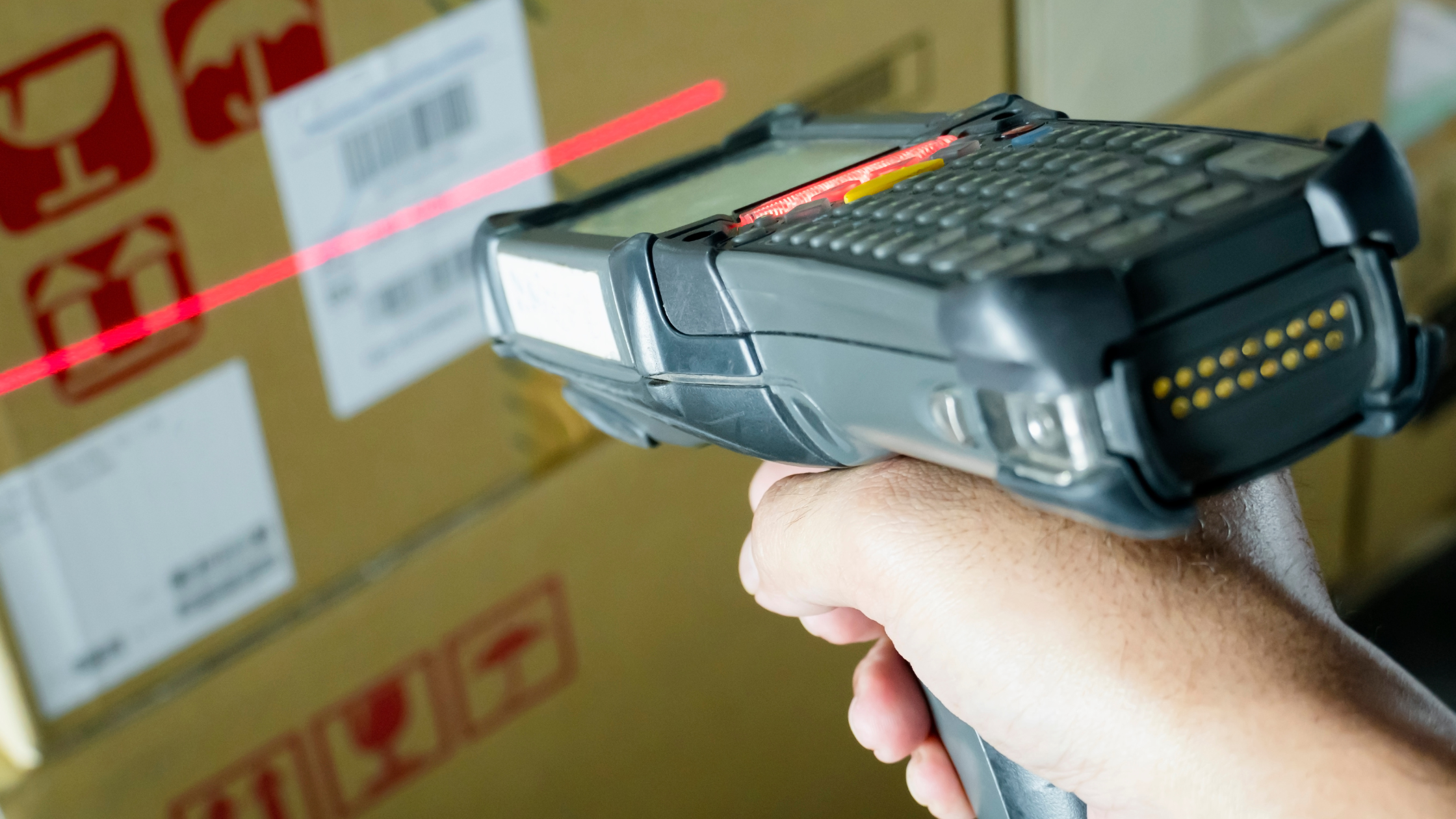
キャムマックスを使った棚管理の基本となるのが、バーコード(QRコード)を活用したロケーション管理の仕組みです。
棚の位置と在庫情報を紐づけて、移動や入出庫を一元管理することが可能です。
運用イメージ
- 各棚に棚番・バーコードを設置 (例:A-01-03)
- 在庫(商品)にもバーコードやQRコードを付与 (SKU別)
- 入出庫時に「棚番 → 在庫」の順でスキャン
- リアルタイムで在庫数を反映
※キャムマックスで管理できる情報には商品名、商品コード、数量、棚番などがあります。
ピッキングの流れ
受注情報よりピッキングリスト(出荷指示書)がリスト化され、作業者はスマートフォンやタブレット端末で確認しながらピッキングを行います。
基本フロー
- 受注情報からピッキングリストを作成
- 作業者はタブレットでリストを確認
- 指示書に従って棚番→在庫の順でバーコードをスキャンしてピッキング
- ステータスを出荷にすることで自動的に在庫数を更新
ピッキングリストに該当しない商品をスキャンした場合はエラーを返すため、出荷ミスを大幅に削減できます。
エリア設定しておけばピッキングルートも最適化され、作業時間が大幅に短縮します。